융통성, 생산성, 품질에서 최상의 솔루션 제공
독일 자르브뤼켄(Saarbrucken) 및 라이프치히(Leipzig)에 2,250명의 직원을 보유하고 있는 뉴할베르그구스(Neue Halberg Guss)는 주철 및 주조 크랭크 샤프트로 제작된 산업용 모터를 위한 실린더 헤드인 원통형 크랭크실을 생산 및 개발하고 있으며, 이 분야와 관련해 유럽시장에서는 리더이자 기술적 선구자다. 
이 제품이 적용되는 적용 범위는 차량을 위한 정교한 3개의 실린더 블록으로부터 상용 차량을 위한 대형의 V8 엔진까지 다양하며, 다른 제품들로는 연성 주철로 제작된 베어링 터널과 알루미늄으로 제작된 대판도 포함한다.
이 회사의 주요 고객사로는 폭스바겐, 다임러, BMW, 아우디, MAN, 스카니아 및 이베코와 같은 잘 알려진 자동차 및 상용 차량 제작사 등이 있다.
이 회사의 자르브뤼켄 공장에서는 크랭크실 코어 패키지의 완전한 조립을 위한 자동화된 솔루션을 찾고 있었으며, 이를 위해 하나의 시스템 내에 많은 수의 쿠카 로봇을 사용하기로 결정했다.
아우쿠스부르크(Augsburg)에 기반을 둔 로봇과 시스템 빌더로부터의 25대 기계들 모두 최상의 정밀도로 완전한 자동화 조립 단계를 수행하고 있다. 현재 총 50대의 쿠카 로봇이 이 두 개의 시스템에서 코어 패키지를 조립하고 있다.
완벽한 조화의 쿠카 로봇 관현악단
뉴할베르그구스의 프로젝트 관리자인 페터 코흐(Peter Koch) 씨는 “경험과 전문성을 갖춘 개발 파트너로서 우리는 제품 아이디어로부터 시리즈 생산 준비에 이르는 과정에서 고객과 함께하고 있다”면서, “완전한 자동화를 기반으로 조립하는 방식을 통해 코어 패키지를 설계하는 것은 특정 도전과제가 될 수도 있다”고 말했다.
여기서 로봇 기반 자동화는 융통성, 생산성, 그리고 품질에서 최상의 솔루션을 제공하고 있다. 크랭크실 코어 패키지의 조립을 위해, 최대 3대의 다른 크기 로봇을 사용했다. 이들 로봇들은 주조공장 환경에서 이상적인 동시에 특히 공간 절감의 효과 및 셀 개념을 허용한다.
이 회사의 포괄적 로봇 포트폴리오 덕분에 쿠카는 방대하고 다양한 작업 단계 및 개별 로봇의 상호작용, 이 두 가지 측면에서 최적의 솔루션을 제공할 수 있었다.
코흐 씨는 “우리가 선택한 쿠카 로봇 모델은 ‘KR AGILUS’ 소형 로봇 시리즈와 ‘KR 5 Arc’, 그리고 KR QUANTEC 시리즈인 ‘KR 300 R2500 Ultra F’였다”고 말했다. 이 회사에서 25대의 로봇은 현재 관현악단처럼 완벽한 조화를 이루며 함께 연동하고 있다. 12대의 KR 300 R2500 Ultra F를 비롯한 11대의 KR 5 Arc, 두 대의 KR 6 R900 Sixx 쿠카 로봇이 2013년 이후부터 지금까지 완전한 자동화를 실현하면서 크랭크실 코어 패키지를 조립하고 있다.
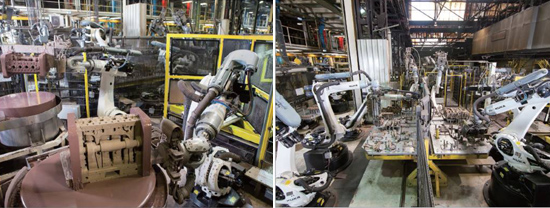
‘조립’이라는 콘서트에서의 이상적인 상호작용
조립 프로세스 내 최초의 로봇은 ‘KR QUANTEC Foundry’ 로봇이다. 이 최초의 로봇은 코어 투입 기계로부터 전체 코어 셋을 제거한다(물 재킷, 밸런스 샤프트, 채널 코어, 물 펌프 코어, 온도조절장치 코어, 휠 코어, 크랭크실 코어 및 단독 코어로 구성). 번호 1과 번호 2 턴테이블에 이들을 설치했으며, 이후에는 더 작은 ‘KR 5 Arc’ 로봇으로 이 턴테이블을 180도 회전시킨다.
부품 조립 및 ‘콘서트’ 디버링을 통해 KR 5 Arc 로봇과 KR AGILUS 로봇이 융통성 있게 실행된다. 받침대와 업라이트 상에 측면 장착된 오버 헤드는 온도 조절기 코어를 디버링 및 조립하고 최상의 정밀도로 물 펌프 내에 구멍을 뚫는다. 이후 휠과 크랭크실 내부, 물 재킷 코어 내부, 그리고 크랭크와 단일 코어 내부에 구멍을 뚫는다. 일단 두 개의 턴테이블을 다시 최초 지점으로 되돌린 후 KR QUANTEC 시리즈인 KUKA 로봇 세 대는 개별 코어를 집어 부분적 조립을 위해 턴테이블 번호 3 위에 세팅한다.
또 다시 180도 회전한 후 두 대의 추가 로봇인 KR 300은 전체적으로 조립된 패키지를 설정하며, 다른 로봇은 패키지를 제거하고 고정나사 조임 스테이션 아래로 그것을 이동시킨다. 나사 조임에 이어 6개의 축 로봇은 턴테이블 번호 4 위에 그것을 세팅하며, 조립된 패키지를 세척 셀을 향해 회전시킨다. 세척 셀에 도달했다면, KR 300은 패키지를 집어 세척을 위해 담근다. 패키지를 축 중심으로 회전하면서 골고루 세척한 다음 패키지에서 세척수가 마를 때까지 둔다.
이러한 세척 프로세스에 90초가 소요되는데, 이는 60초인 코어 패키지 전체 조립보다 더 길기 때문에 두 대의 세척 로봇을 동시에 사용함으로써 이상적인 사이클 시간을 보장하도록 한다.
그 다음에는 세척된 패키지를 다시 턴테이블로 설치하고, 다시 한 번 수동 검수 스테이션을 향해 90도 회전시킨다.
작업자의 검수를 거친 후 앙상블 내의 마지막 로봇은 코어 패키지를 집어 8개의 슬롯을 가진 랙에 설치하는데, 만약 이들 패키지들 모두가 젖었을 경우에는 하이 베이 내 최종 제품들 사이에 배치하기 전 건조 오븐으로 세척된 코어 패키지인 팩을 전달한다.
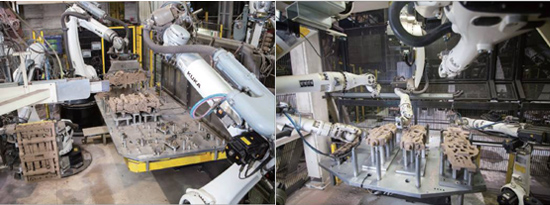
로봇을 통한 조화로운 조합
KR300 R2500 Ultra F 로봇을 통해 뉴할베르그구스는 진정한 주조공장으로서 전문성을 획득했다. QUANTEC Ultra 제품군의 로봇은 시장에서 최대 성능은 물론 최대 스트림 라인설계와 결합된 높은 유상 하중 용량으로 특성화할 수 있다. 이러한 특성은 무거운 워크피스와 높은 정밀도의 기계를 취급할 경우 발휘된다. 주조공장에 적용시 이들 로봇들은 충격에 강하고 부식에 보호된 주조공장 피스톤 핀(산과 알칼리 둘 모두에 대한 저항성이 있음)을 적용할 뿐 아니라, 먼지와 오물에 강하며, 180°C까지의 온도에 견딜 수 있다.
탁월한 정밀도와 융통성 및 속도 덕분에, KR 5 Arc 로봇과 KR AGILUS 로봇은 조립 프로세스 내에서 특히 두드러진다. 동시에 소형 로봇 구획으로부터의 로봇 변종과 낮은 유상 하중 범위는 소형 셀 개념에서 공간 절약 설치라는 이점을 제공한다.
설계 단계시 준비된 로봇 11대의 추가 앙상블
페터 코흐 씨는 “로봇 기반 시스템은 50%의 생산성과 품질 증가를 가져왔다”고 결론지었다.
현재 쿠카 로봇 오케스트라의 각 시스템은 시프트당 약 400개의 코어 패키지를 조립해 생산성을 높일 뿐 아니라, 추가적으로 생산 비용까지 크게 절감시키고 있다.
로봇 기반 자동화 솔루션 역시 자르브뤼켄 공장 내 크랭크실 코어 패키지를 위한 일관된 고품질을 보장한다. 이 시스템은 그리퍼를 교체할 필요 없이 코어 패키지의 두 가지 다른 형식을 조립할 수 있으며, 이때 필요한 모든 것은 문제에 특별한 변화를 가하는 것뿐이다.
뉴할베르그구스사와 그 직원들은 이 솔루션에 매우 만족해하고 있다. 페터 코흐 씨는 “쿠카 로봇을 통한 긍정적 경험 덕분에 우리는 향후 11대의 쿠카 로봇으로 더 작은 앙상블을 가진 추가 시스템을 계획하고 있다”고 언급했으며, 이 로봇 앙상블은 하역, 디버링, 조립 및 세척에 사용될 예정이다.
FA Journal 김 미 선 기자 (fa@infothe.com)
<저작권자 : FA저널 (http://www.fajournal.com) 무단전재-재배포금지>
저작권자 © 인더스트리뉴스 무단전재 및 재배포 금지