항공기 엔진 터빈 검사 위한 솔루션 적용
항공기 엔진에 들어 있는 터빈은 매우 거친 환경에 노출돼 있으며, 한 번에 여러 시간 동안 800℃ 이상의 온도에서 30,000rpm의 속도로 회전한다. 엔진 제조업체들은 아주 경미한 결함조차 성능을 저하하고, 유지보수 비용을 높이며 항공기 엔진의 가용 수명을 단축한다는 점을 이해하고 있다. 즉, 항공 운송업계가 요구하는 효율과 신뢰도를 유지하려면, 이들 제조업체는 터빈 날개를 매우 꼼꼼히 검사해야 한다.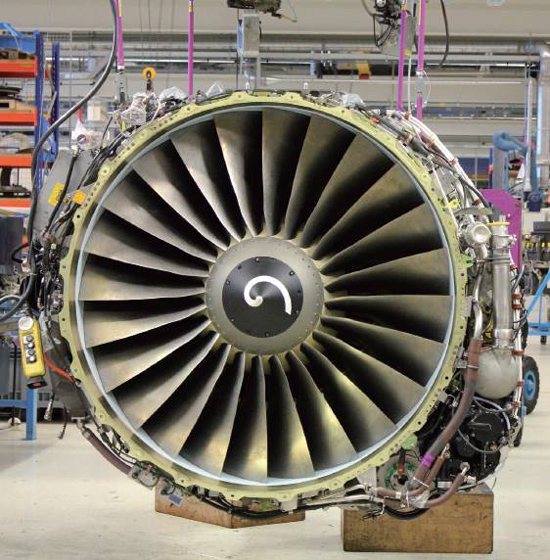
수작업의 한계, 과한 시간 소요와 일관되지 못한 검사 결과
북미 지역의 한 제조업체는 고도의 훈련을 받은 검사 책임자들이 수백 가지 특성을 측정하고, 수천분의 1인치 깊이에 숨어 있는 표면 결함을 점검하는 방식, 즉 손과 눈으로 날개를 검사했다. 그러나 이러한 수작업에 의한 검사는 시간과 노동력 차원에서 비용이 많이 들 뿐만 아니라 주관적이라는 문제점이 있었다. 그 때문에 검사 결과는 다양하게 나타났으며, 심지어 검사 담당자들 사이에서도 차이가 있었다. 마지막엔 수작업에 의한 검사에 너무 많은 시간이 소요돼 모든 날개를 체계적으로 검사하지 못하고 몇몇 샘플만 검사한 경우도 있었다. 확실히 제조업체에는 날개의 체계적인 검사, 시간 절감, 그리고 일관되고 반복 가능한 결과를 도출하는 검사 방식이 필요한 상황이었다.
복잡한 분석. 인터페이스와 편리함, 정밀함으로 돌파
그 때문에 이들은 퀘벡 라발에 위치한 오루스인테그레이션(Orus Integration Inc)에 터빈 검사 시스템 개발을 의뢰했다. 당시 상황에 대해 오루스인테그레이션 루이 디케어(Louis Dicaire) 프로젝트 매니저는 “개발팀은 프로젝트 초반에 성공을 위해선 융통성, 반복 가능성, 정밀성이 꼭 필요하단 점을 배웠다”고 언급했다. 오루스의 엔지니어링 팀은 개발 당시 이전 경험에 의존했다.
![]() | ||
루이 프로젝트 매니저에 따르면 계측 장비 설계와 관련해 어려운 점은 반복 가능성, 정밀성, 그리고 선형성 확보로 항상 같다. 그리고 시스템이 예측 및 반복 가능한 결과를 반환하도록 하려면 소프트웨어는 정밀한 서브픽셀 정확도를 갖춰야 하며, 장비는 5 마이크론 미만에 +/- 3 Sigma의 정밀도로 계측 가능하다. 물론 이미지는 조명의 영향을 많이 받으며 시스템에 안정적인 고성능 광학 시스템이 필요하다.
오루스 측은 필요한 정밀도를 확보하고자 군 장비 수준의 보정용 타깃을 사용, 측정 스테이션의 카메라도 모두 한꺼번에 보정했다. 그 결과 INL-1900x2T는 수천 명의 인력 절감 효과를 제공하면서, 매우 복잡한 분석을 수행할 수 있고, 조작자에게 단순한 인터페이스와 사용하기 쉬운 콘셉트를 제공할 수 있는 장점을 갖추게 됐다.
솔루션 구성과 장점
INL-1900x2T에는 한 개의 하우징을 검사하는 두 대의 스테이션이 들어 있다. 계측 스테이션에는 1,920×1,080 해상도에 각각 넓은 시야의 텔레센트릭 렌즈가 장착된 Basler pilot GigE 카메라 두 대, 청색 LED(520nm) 조명 두 대가 장착돼 있고, 표면 검사용 스테이션은 네 대의 Basler pilot GigE 카메라가 장착돼있다.
1차 표면 검사 카메라의 해상도는 1,920×1,080이며 나머지 카메라 세 대는 640×480 해상도로 한 대의 카메라로는 포착하기 어려운 영역에 대한 표면 검사를 수행한다. 두 대의 CS Diffuse on-Axis 조명과 한 대의 CCD 확산 백라이트는 표면 검사용 스테이션에 사용된다. 그리고 하드웨어 구성 부품에는 Fanuc-6-Axis LR Mate 200iC 로봇과 4U 컨트롤러, 그리고 Omron PLC가 포함되며, 소프트웨어는 프로세싱 팩 1(Processing Pack 1)이 포함된 Matrox Imaging Library(MIL) 9.0을 바탕으로 한다. 또한 INL-1900x2T는 카메라의 텔레센트릭 렌즈, 열과 진동을 흡수하는 4인치 화강암 석판을 갖춰서 매우 안정적인 광학 시스템 성능을 보인다.
![]() | ||
INL-1900x2T는 3가지 검사 역할을 수행한다. 먼저 날개의 수백 가지 계측 특성을 확인하고, 터빈 날개의 양면과 기타 중요한 표면의 결함을 검사하고, 부품의 글자 마킹을 확인한다. 전체 검사 과정은 부품당 15초가 걸린다.
일괄검사를 수행하려면 조작자가 먼저 작업 내용 지시서의 바코드를 스캔하고 부품을 고정하는 원형 컨베이어를 통해 포켓 휠을 적재해야 한다. 그러면 높이 감지기가 Y 위치를 확인해 부품이 올바로 적재됐는지 확인하는 동안, 휠이 첫 번째 부품을 찾는다. 그다음엔 로봇이 날개 부분으로 부품을 픽업해 두 개의 평행광이 비추고 있는 계측 스테이션으로 운반한다. 루이 프로젝트 매니저는 이에 대해 “이런 조건에서 매우 반짝이는 물체의 둥근 부분의 대비는 아주 선명하게 보인다. 하지만 로봇은 반복 수행 능력은 뛰어나지만, 날개를 우리가 필요로 하는 10마이크론 미만의 정밀도로 배치하지는 못한다는 점도 알아야 한다”고 강조했다.
이 애플리케이션에서 정밀도는 극히 중요하다. 오루스의 솔루션은 부품을 회전시켜 고속으로 이미지를 촬영하는 것이었다. 측정해야 할 특성에 따라 소프트웨어는 구체적인 특성을 최소화하거나 최대화하고, 기준점이라 불리는 특정 참조점의 이미지가 원본 CAD 드로잉과 일치하면 소프트웨어가 이것을 참조 이미지로 식별한다. 그 다음 계측 소프트웨어가 부품의 평행도, 길이, 반경, 각도, 기타 특성을 측정하는데, 사실 최적화해야 할 기준점이 많기 때문에 이 단계는 두 번 이상 수행된다.
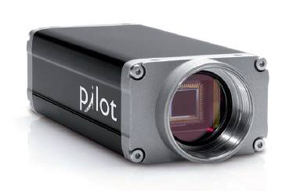
검사가 완료되면 모든 부품 검사 결과가 기록되고, 모든 데이터를 보고에 사용할 수 있다. 부품이 검사를 통과하면 로봇이 해당 부품을 ‘우수 부품’ 이송로에 떨어뜨리고, 특성 검사에 불합격했을 경우 부품은 집게에 고정되며 해당 부품에서 보정해야 할 것이 무언인지 조작자가 알 수 있도록 화면에 정보가 표시된 뒤, 그리퍼가 부품을 불량품 이송로에 떨어뜨린다.
그리고 휠이 회전하고, 다음 부품을 색인화하고 원형 컨베이어의 모든 부품에 대해 검사 공정이 반복 수행된다.
<바슬러 제공>
FA Journal 편집국 (fa@infothe.com)
<저작권자 : FA저널 (http://www.fajournal.com) 무단전재-재배포금지>
저작권자 © 인더스트리뉴스 무단전재 및 재배포 금지