공정별 맞춤형 데이터 수집으로 업무 효율 ‘UP’!
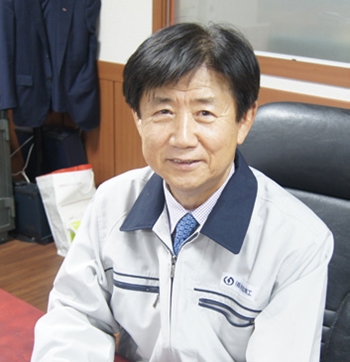
스마트공장을 도입하게 된 계기는?
금형생산은 매 수주마다 다양한 고객의 요구사항을 맞춰야 함에 따라 공정의 자동화는 사실상 불가능한 영역이며 작업자가 모든 공정을 직접 수행하는 생산 방식이다. 그동안 금형 산업에 적용된 대부분이 공정관리시스템(MES)이 경영진 및 관리부서에는 업무 및 정보관리 효율화 측면에서 좋은 효과를 제시했으나 비즈니스 성과 지표 산출을 위한 실 데이터 영역인 생산실적을 반영함에 있어 작업자에게 수동 입력을 요구해야 하는 단점을 갖고 있었다.
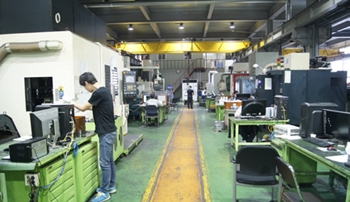
설비가동률 10% 향상 기대
스마트공장 시스템 도입 전에는 작업일보를 통해 작업 실적 집계는 가능했으나 설비의 실가공 시간 산출은 불가능했다. 이로 인해 설비가동률 집계가 사실상 불가능해 실질적인 설비관리가 안 되고 있었다.
설비가동률 산출을 위해 지난 5월말 POP 구축을 완료해 6월부터 3개월간 산출요소 수집을 위해 설비 실가동 시간을 수집했으며 산출결과 사업계획 당시 예상한 60%보다 낮은 55.2% 수준을 보여주고 있다.
건우정공은 설비가동률을 높이기 위해 공정관리팀과 CAM팀이 노력을 했으나 해당 산출기간 내 여름휴가 기간이 겹쳤으며 신규 가공물량보다는 마무리 작업이 많았던 시기였다.
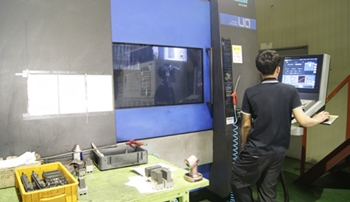
공정을 확인하고 있는 모습
건우정공은 스마트공장 구축으로 기존에 측정 불가했던 설비모니터링의 가동상태 확인 및 장애, 문제 발생시 작업자 보고에 의존했던 것을 공정관리자 PC 화면을 통해 설비 상태를 실시간으로 모니터링을 할 수 있게 됐다. 이러한 모니터링에 의해 장애, 대기 발생시 공정관리팀의 즉각 대응도 할 수 있어 작업 효율이 높아졌다.
설비종합효율에서는 POP를 통한 설비 실가동 현황을 수집하고 작업일보 디지털화로 실적 데이터를 자동집계 할 수 있게 됐다. 이에 설비모니터링 및 설비종합효율 가동률, 생산성 극대화 체계 마련이 가능해졌다.
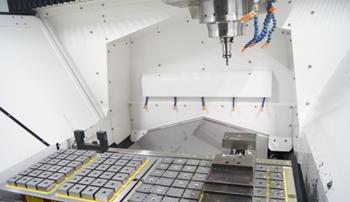
건우정공의 스마트공장 구축은 올해 1월 시작으로 아직까지 완성 단계는 아니다. 하지만 현재 각 공정별 데이터를 수집하고 이를 분석하는 단계에 있으며 앞으로의 변화가 기대된다.
우선 작업의 간소화로 인한 작업자들의 업무 효율 향상이 기대된다. 기존에는 각 공정별 데이터를 직접 수기로 작성해야 했기 때문에 자칫 잊고 지나치는 일이 빈번히 발생해 기계 오류나 제품 불량이 발생했을 경우 대처하기가 어려웠다. 이에 작업자들 또한 제조 업무에만 집중하기 어려워 수년간 생산 효율이 크게 달라지지 않았다.
그러나 스마트공장 구축 후에는 각 설비별로 데이터를 수집할 수 있는 장치가 설치돼 있어 자동으로 각종 정보를 수집, 분석할 수 있게 돼 업무효율 상승이 기대된다. 돌발 상황 대처 역시 기존에는 숙련된 작업자들만이 해결할 수 있었던 것을 미리 설비에 입력함으로써 대처 시간 단축과 다양한 방법으로 해결할 수 있게 됐다.
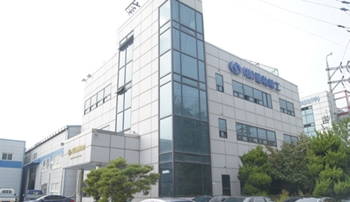
건우정공은 1, 2차에 걸쳐 스마트공장 구축을 진행했다. 현재는 금형생산 통합 관리시스템 구축으로 제작 효율 향상이 기대된다.
통합 관리시스템은 금형 가공설비 실운용 현황 실시간 모니터링과 금형 생산설비와 공정관리 효율화를 위한 생산설비 CAPA 및 가동률 관리 체계, 생산공정 이슈 및 이벤트에 대한 실시간 알람, 금형 기술문서 산출물의 중앙화 관리 및 온라인 협업 체계 구축 등이다.
이에 대한 기대효과로는 건우정공이 보유 전 생산설비의 가동률 관리에 따른 설비능력 극대화와 금형 부품 실시간 생산·설비능력 관리를 통한 효율적인 공정관리 가능으로 생산성 향상 및 효율증대에 따른 납기 단축이다. 또한 금형개발 산출물의 중앙화 및 이력관리에 따른 협업능력 향상, 데이터 관리 효율성 및 업무 생산성 증대 등이 있으며 신속하고 효율적인 생산관리 체계 구축으로 제조경쟁력 향상에 따른 매출 및 이익 증대가 기대된다.
FA저널 SMART FACTORY 박 규 찬 기자 (fa@infothe.com)
<저작권자 : FA저널 SMART FACTORY (http://www.fajournal.com) 무단전재-재배포금지>
저작권자 © 인더스트리뉴스 무단전재 및 재배포 금지