전 세계 자동차 제조업체의 품질 향상에 기여하다
자동차는 거의 대부분 컴포넌트나 서브 어셈블리 또는 주요 시스템에 이르기까지 모든 구성요소들을 머신비전 기술을 이용해 추적, 조립, 검사를 수행한다. 짧은 리드 타임과 타이트한 재고관리, 전 세계를 넘나드는 복잡한 공급망과 OEM의 제로 결함 요구에 부응하기 위해 자동차 제조업체들은 생산시설 전반에 머신비전 기술을 적용함으로써 이를 해결해 나가고 있다.
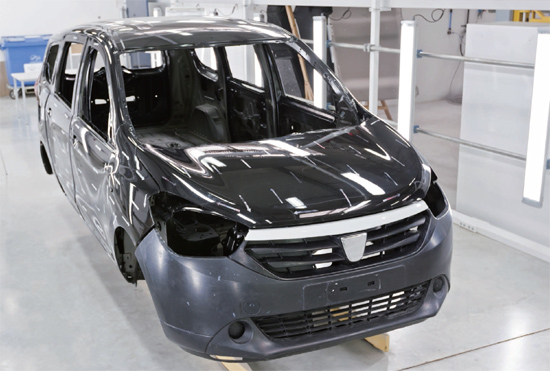
코그넥스(Cognex)의 머신비전 제품은 전 세계 수많은 선도적인 자동차 제조업체들과 공급업체, 머신 빌더들이 자동차산업의 엄격한 품질요건에 부합하는 제품을 공급하기 위해 사용하고 있다.
코그넥스 비전머신 기술은 기업들이 생산의 모든 단계에 걸쳐 결함을 제거하고, 조립 검증과 정보 수집 및 이력추적을 통해 제조품질과 성능을 향상시키는 데 도움을 준다. 따라서 코그넥스 비전 기술을 이용한 보다 스마트한 자동화를 구현함으로써 생산 오류를 줄이는 것은 물론, 이를 통해 제조비용을 절감하고 고객 만족을 더욱 향상시킬 수 있다.
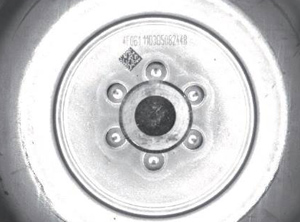
향상
제조공정 전반에 걸쳐 신속하고 정확한 데이터 관리는 효과적인 생산이력 및 공정관리는 물론 생산성 증대 및 품질 향상에 있어 매우 중요하다. 지난 2001년 국내 최초의 자동변속기 전문 기업으로 설립된 현대자동차그룹의 자회사인 현대파워텍은 보다 신속한 생산이력 및 공정관리를 달성하기 위해 8속 후륜 자동미션 라인의 까다로운 판독 조건 및 DPM(Direct Part Mark) 2D 코드에 대응할 수 있는 높은 판독률의 ID 리더기를 필요로 했다.
8속 미션은 부품이 복잡해지고 소형화되면서 레이저로 마킹되는 2D DPM Data Matrix 코드 또한 매우 작은데다, 자동차 제조업체별로 다양한 모델의 미션을 생산해야 하기 때문에 부품의 형태나 모양이 각기 다르고 2D 코드의 위치도 유동성이 매우 심해 안정적인 재연성과 높은 판독률을 달성하기 어렵다.
현대파워텍은 이러한 요건을 충족시키기 위해 여러 공급업체의 ID 리더기에 대한 데모를 진행했다. 그 결과, 다른 경쟁사 제품들은 70% 미만의 판독률을 보인 반면, 코그넥스의 ID 리더기는 100%의 판독률을 달성했으며, 재연성 테스트에서도 100% 안정성을 보임으로써 최고의 ID 리더기로 채택됐다.
현대파워텍은 코그넥스의 고해상도 카메라 기반 ID 전용 모델인 ‘In-Sight 5413’과 유선 타입의 ‘DataMan 8500’, 그리고 VisionPro Max의 다양한 ID 툴 라이브러리를 사용하고 있으며, 8속 후륜 자동미션 라인을 비롯해 무단변속기(CVT), 6속 자동미션 라인에 모두 코그넥스 솔루션을 사용하고 있다.

기아자동차, 6속 미션 생산라인에서 99%의 판독률 달성
자동차산업의 이력관리는 제조과정에서 엄격한 품질관리는 물론 공정을 최적화하고 비용을 절감할 수 있을 뿐만 아니라, 공급체인 전반에 걸쳐 특정 차량 및 관련 부품들을 자료화함으로써 향후 발생할 수 있는 품질보증 및 리콜 문제 등에 정확하고 신속하게 대처할 수 있도록 해준다. 이러한 이력관리는 각 컴포넌트들에 마킹된 2D Data Matrix 코드에 저장된 주요 생산정보를 바탕으로 이뤄진다.
기아자동차는 2D Data Matrix 코드를 이용해 엔진 및 미션의 구성부품들의 이력관리를 수행하고 있다. 하루에 1,800개의 미션을 생산하는 기아자동차 기존 미션 라인의 코드 판독률은 96~97%에 머물렀고, 일일 생산량이 1,300~1,400개에 이르는 엔진라인의 경우에는 판독률이 97%를 넘지 못했다. 만약 이러한 생산라인에서 판독률을 2~3% 향상시킬 수 있다면 작업 효율은 물론 생산수율 향상, 제조비용 절감 등 여러 가지 이점을 얻을 수 있다.
판독률이 낮은 ID 리더기는 잦은 판독 불가 상황을 유발해 라인을 중단시킬 뿐 아니라, 작업자가 직접 수동으로 조작해야 하기 때문에 공정의 사이클 타임을 맞출 수 없어 작업 효율 및 생산수율을 떨어뜨리며, 심지어 적합하지 못한 부품이 조립돼 불량을 초래할 수도 있다. 특히, 6속 부품들은 더욱 복잡하고 그 수도 많은데다 크기도 작기 때문에 판독이 더욱 까다롭다.
기아자동차는 이러한 문제를 해결하기 위해 6속 라인에 코그넥스의 In-Sight 시스템과 DataMan ID 리더기를 도입함으로써 99%의 판독률을 달성하는 데 성공했다. 코그넥스의 ID 리더기는 가장 까다로운 DPM 및 라벨 기반 ID 애플리케이션에서 최고의 판독률(99.9%)을 달성할 수 있도록 특허받은 알고리즘으로 최적화돼 있다.
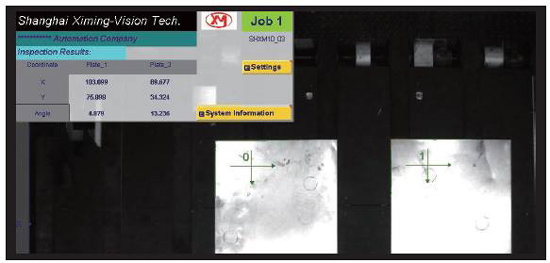
BMW 브릴리언스 오토모티브, PatMax 알고리즘으로 정확도 향상
BMW 브릴리언스 오토모티브(BMW Brilliance Automotive)는 BMW그룹과 브릴리언스자동차그룹(Brilliance Auto Group)의 합작회사로 지난 2003년 5월에 설립됐으며, BMW 자동차의 생산 및 판매, AS 서비스를 담당하고 있다.
이 회사의 생산기지는 중국 요령의 선양(Shenyang)에 위치해 있으며, 베이징 지사를 비롯해 중국 전역에 걸쳐 판매 및 서비스 네트워크를 갖추고 있다.
이 회사의 자동차 강판 포지셔닝 공정에서 무게 중심 및 기계식 센터링 작업은 모두 동일한 문제를 안고 있었다. 첫 번째는 중력 및 실린더 팻(Cylinder Pat)으로 품질에 영향을 미치는 손상이 제품의 외관에 남게 될 수 있으며, 두 번째는 생산라인이 중력 및 기계식 래핑으로 인해 영향을 받는다는 것이다. 그리고 세 번째는 비용이 너무 높다는 것이다.
비전 방식의 위치 확인은 이러한 문제를 쉽게 해결할 수 있다. 먼저, 비전 방식의 위치 확인은 비접촉식으로 이뤄지기 때문에 손상이 발생하지 않는다. 비전 시스템은 컨베이어 벨트 위에 설치되기 때문에 외력의 증가로 인한 품질 손상을 방지할 수 있다. 두 번째 장점은 로봇에 좌표 정보를 제공하기 위해 사진을 찍고 이미지를 처리하기까지 시간이 불과 50밀리초밖에 걸리지 않는다. 세 번째는 기존의 위치 확인 방식과 비교할 경우 비전식 위치 확인은 비용 절감이 가능하면서도 안정성 및 정밀도를 높일 수 있다.
모든 머신비전 애플리케이션의 첫 단계이자 성공의 핵심은 비전 카메라의 시야각 내에 물체를 위치시키는 것이며, 이 프로세스를 ‘패턴 매칭’이라고 부른다. 많은 변수들이 영향을 미칠 수 있기 때문에 패턴 매칭은 매우 어렵다. 전통적인 패턴 매칭 기술은 픽셀 그리드 분석 프로세스에 기반하고 있는데, 이 방법은 특정 상황에서는 효과적이지만, 생산라인의 외관이 자주 변경되는 경우에는 객체의 위치 확인 성능 및 정확성에 한계가 있다.
BMW 브릴리언스 오토모티브는 이러한 한계를 극복하기 위해 코그넥스의 PatMax 기하학 패턴 매칭 기술을 활용했다. 이 알고리즘은 객체의 기하학 모양을 픽셀 그리드에 기반을 두지 않고 경계 곡선으로 얻을 수 있으며, 특정 그레이 레벨에 제한되지 않는다. 따라서 객체의 각도나 크기, 모양이 바뀌더라도 상관없이 정확하게 해당 객체를 찾을 수 있다.
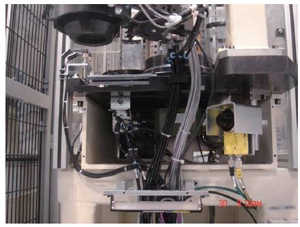
코그넥스의 비전 시스템
1933년에 설립된 닛산모터(NISSAN Motor Corporation)는 일본의 3대 자동차 제조업체 중 하나이자 세계 10위권의 자동차 기업이다. 세계 최초로 소형 세단인 닷산(Datsun)을 출시한 바 있으며, 자동차 부품 및 컴포넌트도 생산하고 있다.
또한, 이 회사는 자동차 생산과 더불어 다양한 머신 툴 및 엔지니어링 머시너리, 조선, 우주항공 기술 분야에서도 대규모 다국적 기업으로 잘 알려져 있다.
닛산은 제품 품질을 위해 항상 엄격한 요건을 적용하고 있으며, 생산공정을 향상시키기 위해 지속적으로 노력하고 있다. 이 회사는 결함을 방지하고, 식별하기 위해 자동차 엔진 조립라인에 비전 시스템을 적용해 무결함 목표를 달성할 수 있는 자동차 생산공정을 구축하고 있다.
이 엔진 조립라인에 피스톤 링을 설치하기 위해 서로 다른 모델의 2개 피스톤 링이 각 엔진의 피스톤에 필요하다. 비전 시스템은 피스톤 링에 마킹된 컬러를 이용해 피스톤 링의 누락 또는 부적합 여부, 반전 상태 등을 인식하고 판별해야 하며, 결과를 ProfiNet 프로토콜을 통해 PLC로 전송해야 한다. 닛산은 코그넥스의 ‘In-Sight 5100C’를 채택해 서로 다른 컬러 및 위치 판독을 통해 피스톤 링을 정확하게 구별하고 식별할 수 있게 됐다.
이전의 엔진 조립라인은 반자동이었기 때문에 피스톤 링 검출은 사람의 눈으로 직접 판독해야만 했다. 하지만 작업자의 집중력이 떨어지고 피로하게 되면 부속물의 부적합, 누락, 반전 등의 문제는 물론 다른 품질사고를 야기할 수 있다. 닛산모터는 코그넥스의 In-Sight 비전 시스템과 더불어 최신 컬러 추출 툴인 ExtractColor를 이용해 지정된 컬러와의 매칭 여부를 완벽하게 식별함으로써 생산품질의 무결함 목표를 달성할 수 있게 됐다.
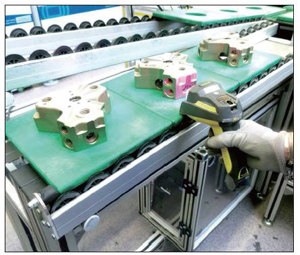
판독 작업을 수행할 수 있다.
자동차 부품 제조업체 및 공급업체들은 고객들에게 제품을 선적하기 전에 중대한 결함을 모두 점검할 수 있는 기술을 필요로 한다. 특히, 허용 편차가 수 마이크로미터에 불과한 부품의 경우에는 거의 완벽한 정확도로 검사를 수행할 수 있어야 한다.
보쉬디젤(Bosch Diesel)은 제품의 품질 검사는 물론 모든 컴포넌트의 이력을 추적하기 위해 코그넥스의 머신비전 시스템과 바코드 리더기를 채택했다.
코그넥스 바코드 리더기 및 비전 시스템이 제공하는 가장 큰 혜택은 모든 핵심 작업공정의 전 생산라인에 걸쳐 컴포넌트(펌프 바디)의 이력을 추적할 수 있다는 것이다. 생산요건에 따라 각각의 특성들이 Data Matrix 코드를 이용해 기록되며, 생산공정에서 기록된 이미지는 재확인을 위해 차후 이용이 가능하다.
특히, 코그넥스 비전 시스템 및 바코드 리더기는 설정 툴을 이용해 매우 간편하게 프로그램을 설치할 수 있다. 또한, In-Sight Explorer 소프트웨어에서 제공되는 스프레드시트 프로그래밍 인터페이스를 사용하면, 안정적이면서도 효율적인 방법으로 비전 툴을 설정하고, 해당 애플리케이션에서 생성된 데이터를 처리할 수 있다.
보쉬의 CP 3 차체 생산라인에서만 약 80대의 바코드 리더기와 25대 이상의 비전 시스템이 적용돼 있으며, 전체 보쉬 생산설비에는 이보다 훨씬 많은 시스템이 설치돼 있다. CP 3 사업부에서 코그넥스 바코드 리더기 및 비전 시스템은 12개 영역의 생산라인에서 작업 및 가공을 제어하는 데 사용된다. 주요 작업은 펌프 바디나 다른 제품 생산상의 결함을 제거하는 것이며, 만약 결함이 감지되면 원인을 식별한다. 이를 통해 보쉬는 결함 있는 제품이 다음 스테이션으로 넘어가는 것을 방지하고, 동시에 오류 지점도 확인할 수 있다.
DataMan 바코드 리더기는 6mm Data Matrix 코드의 가독성을 제어하는 데 사용된다. 결함 판독 성공률은 코그넥스 비전 시스템 및 바코드 리더기를 사용하기 전에는 85%에 불과했지만, 현재 99~100%까지 향상됐다.
FA Journal 김 미 선 기자 (fa@infothe.com)
<저작권자 : FA저널 (http://www.fajournal.com) 무단전재-재배포금지>
저작권자 © 인더스트리뉴스 무단전재 및 재배포 금지