생산 설비 중 데이터 수집이 가능한 PLC, DCS 시스템은?
[스마트제조혁신추진단 박한구 단장] 우리나라 제조기업의 경우 2000년 이전에 도입된 생산 장비들은 아날로그 방식 혹은 메이커 전용의 통신 방식으로 장치에 부착된 측정 데이터를 수집저장 하는데 비용대비 경제적 효과가 미흡해 수집할 필요가 없다. 90년대부터 대용량의 데이터를 PoP와 PLC, PLC와 PLC 간의 통신하기 위해 필드버스(Fieldbus)라는 개념으로 산업현장에 적용해 왔다. 우리나라에 본격적으로 도입된 필드버스는 2000년대로, 그동안 메이커 전용의 통신 표준에서 국제 표준의 필드 버스 표준을 PLC, DCS 제어 시스템에서 채택하면서 제어 시스템 간, 상·하위 시스템 간에 대용량의 데이터를 송수신할 수 있었다.
![스마트제조를 위해서 현장의 디지털화를 통해 Raw Data를 효과적으로 확보하고 관리하는 일이 중요해지고 있다. [사진=utoimage]](/news/photo/202008/39307_35757_628.jpg)
일반적으로 국제 표준의 통신 방식을 채택하고 있는 필드 버스는 CAN, Device Net, Profibus, CC-link, Interbus, EtherCAT, ControlNet, Modbus, Foundation Fieldbus 등 다양하다. 이들과 같은 필드 버스를 채택하고 있는 PLC, DCS 제어 시스템들은 다른 필드 버스와 통신을 할 수 있고 데이터 수집용 PC(DaQ: Data Acquisition System)와 쉽게 통신하면서 PLC, DCS 제어 시스템에서 측정하는 모든 센서 데이터와 내부 설정 데이터를 실시간으로 통신하면서 수집 저장할 수 있다.
반도체를 생산하는 화학 증착장비, 식각장비, 포토 레지스트, 플루오린 폴리이미드 등 고정밀 장비들의 경우, 제조사에서 반도체 장비의 노하우를 복제해 장비를 만들 수 없도록 운전 시에 필요한 데이터만 공개하고, 나머지 장비를 제어하는 데이터는 철저하게 블랙박스화되어 일반 사용자들은 접근할 수 없게 돼 있다. 사용자는 반도체 제조 장비가 고장 혹은 열화로 품질 불량이 발생하게 되면, 지금까지 생산된 반도체를 모두 폐기하기 때문에 사용자는 가능한 반도체 제조 장비의 고장 및 품질을 예측하기 위해 사용자가 장비 제조사와 관계없이 별도의 센서를 추가해 설치하던가, 부착된 센서로부터 데이터 수집하기 위해 센서 신호 분리기를 사용해 데이터를 수집·저장 및 분석하기도 한다.
일반적인 주조, 금형, 용접, 소성가공, 표면처리, 열처리, 단조, 절단 및 절삭 가공 등 중견·중소기업에서 부품을 가공 조립하는 설비의 경우, PLC, DCS 제어 시스템이 국제 표준의 필드 버스 통신 방식을 사용하는 경우에 수집 저장해 디지털화한다. 메이커 전용, 혹은 아날로그 방식의 제어 시스템은 특별한 경우를 제외하고는 수집‧저장하는 것을 권장하지 않는다.
특히 사용자들이 맨눈으로 상태를 보면서 기계를 작동하는 경우 가능한 센서를 부착해, 기계를 자동으로 작동하도록 공정을 자동화하고, 자동화시 필드 버스를 채택하는 PLC를 반드시 선정해 도입해야 한다.
누가 기존 PLC, DCS에서 데이터 수집할 수 있는가?
기존에 운영 중인 PLC, DCS 시스템이 수집 가능한 필드 버스나 RS 232C 등 국제 표준의 통신 방식을 채택하고 있는 경우, 센서 리스트, PLC IO 리스트와 제어 기능을 알고 있는 PLC 엔지니어와 DaQ 수집저장 시스템을 구축하는 DaQ 엔지니어, 제조 공정을 잘 알고 있는 공정 및 설비 엔지니어가 함께 협업해 구축해야 한다. 공정에서 측정되는 모든 센서 속성(사양, 단위, 설치 위치, 용도 등)을 정의하고, PLC 시스템에서 설정하는 데이터, 필요하면 내부 데이터, 소재 데이터 등 생산공장에서 생성되는 모든 데이터를 수집·저장하도록 설계한다. PLC 제어 주기로 DaQ에서 수집하는 소프트웨어를 개발하고, Time Series DB로 저장한다, 가능하면 빅 데이터베이스를 클라우드에 저장해, 향후 AI 솔루션을 쉽게 적용하도록 권장한다.
![제조산업에서의 제조 Raw Data 수집 저장 과정 [사진=스마트제조혁신추진단]](/news/photo/202008/39307_35758_840.jpg)
MES를 도입하기 전에 생산공장을 먼저 디지털화하라!
50인 이하의 중소기업들이 대부분 스마트공장 보급확산 사업에 참여하고 있으나, 실제로 제조기업에 MES나 ERP의 도입보다는 생산 현장의 단순 반복 작업을 자동화하면서 제조 Raw Data를 수집 저장하는 디지털화를 동시에 추진하는 것을 권장한다. MES를 도입하면서 작업자에게 부하 경감을 하면서 효율적인 생산관리를 수행해야 하나, 도입 후 작업자는 작업한 결과를 MES에 입력해야 추가적인 일이 발생하고 있다. 작업자가 입력하는 대신, 센서를 부착하던가, 수작업을 자동화하면, 작업자는 편리해 지속 사용하게 된다.
그동안 2001년부터 ERP, PLM, MES, PoP 등 정부 지원사업으로 많은 기업이 도입해 왔지만, 몇 년이 지나 실제 사용하는 기업은 많지 않은 것 같다. 그 이유는 여러 가지가 있지만, 핵심적인 것은 작업 효율성을 높이기보다, 작업자를 불편하게 만들기 때문이다. 스마트 보급확산 사업은 다음 그림과 같이 열간단조 공장을 예를 들어 설명한다. 3대의 로봇을 이용해 소재를 자동으로 열처리 로에 공급하고, 자동 열처리된 소재를 로봇으로 열간단조 설비에 공급해 단조하면, 바로 로봇으로 추출하는 공정으로 자동화한다. 자동화하면서 로봇, 열처리로, 단조 설비로부터 측정되는 모든 데이터와 운전자 설정 데이터, 단조 후 형상 측정 데이터, 소재, 제품 데이터를 수집·저장하는 디지털화를 수행하는 것이 스마트공장으로 가는 첫걸음이다.
제조 Raw Data는 클라우드 플랫폼에 저장하라
제조 Raw Data는 제어 주기와 동일하게 100ms(1/1,000초)~1초 주기로 수집·저장하기 때문에 시간이 지날수록 데이터 저장 용량이 기하급수적으로 늘어나기 때문에 자체 전산실의 DB Server에 저장하게 되면, 늘어날 양의 디스크를 미리 구매하던가, 매년 필요한 디스크를 추가 구매해야 하는데 비경제적이다. 또한, 5년 이상 사용하게 되면 열화된 컴퓨터 및 디스크 장치를 교체하는 비용이 또 소요된다.
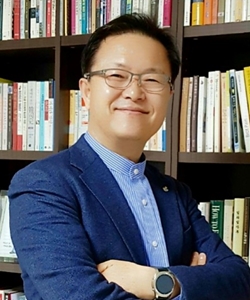
이를 해결하는 방법은 클라우드 서비스 공급회사에서 제공하는 클라우드 컴퓨팅의 데이터베이스에 저장함하는 것이다. 이는 매월 사용한 만큼의 사용료를 내면 되기 때문에 매우 경제적이다. 클라우드에 저장하면 보안이 더욱 강화되고, 1년 이상의 데이터가 축적되어 있으면 AI 솔루션을 도입해 데이터의 가치를 쉽게 얻을 수 있기 때문이다. 클라우드 플랫폼에 빅 데이터베이스를 구축하게 되면 스마트공장 보급확산 사업으로 3년간의 사용료를 지원하고 있다.
글 스마트제조혁신추진단 박한구 단장