TIA Portal PLCSIM Advanced를 활용한 가상 시운전 솔루션
[FA저널 SMART FACTORY 이건오 기자] 지난 2월호 엑스퍼트칼럼 첫 연재에서는 통합 엔지니어링 툴을 이용한 장비 개발 트렌드를 설명하며, 스마트 팩토리의 필수불가결한 하나의 핵심 요소가 통합 자동화라고 정리했다. 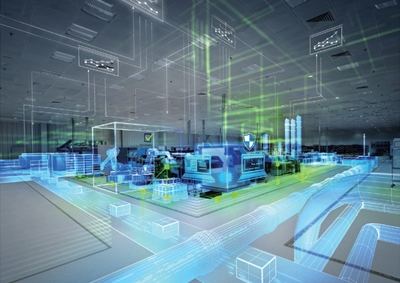
연재 순서
1. TIA Portal 모션 통합에 의한 장비 개발 솔루션
2. TIA Portal PLCSIM Advanced를 활용한 가상 시운전 솔루션
3. TIA Portal Energy Suit를 통한 에너지 데이터 통합
4. TIA Portal통합 엔지니어링과 OPC UA를 통한 디지털공장 구축 사례
지멘스 제공
이번 3월호에는 Industry 4.0 Digital Workflow의 한 축인 가상시운전(Virtual Commissioning) 콘셉트에 대해 다뤄 보고자 한다. 이해를 돕기 위해 3기의 PLC, 60기의 서보 모터 및 드라이브, 2기의 팔렛타이징 로봇 및 상응하는 개수의 컨베이어, 장비 개발 기간을 포함한 현장 설치 시운전 시간 4개월의 상황을 가정하기로 한다.
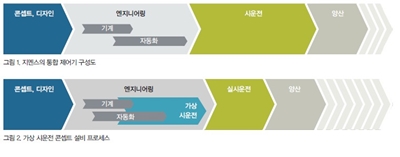
이 기간 중 가장 예측 불가능하며, 문제가 발생 했을 때 양산까지의 소용 시간에 가장 큰 영향을 미칠 수 있는 시점은 바로 현장 시운전 기간이다. 설계 과정에서 예측하지 않은 기구 간섭이 생길 수도 있고, 액추에이터 혹은 로봇의 충돌로 파손된 기계파트를 새로 주문해서 교체하는 시간에 일정이 지체 될 수도 있다.
만약 시운전 지체 시간을 줄이고, 문제점들의 발생 가능성을 최소화해 최적의 생산 조건을 미리 예측하고, 4개월의 프로젝트 기간을 3개월로 줄일 수 있다면 이론적으로는 25% 가량의 시운전 인건비와 그에 상당하는 기회비용을 절감할 수 있을 것이다. 또한 이 기간은 고스란히 생산성 향상으로 이뤄져 매출 및 마진의 향상으로 연결 될 것이다.
물론 위에 설명한 예는 너무 극단적인 계산으로 접근한 것일 수 있다. 그러나 피할 수 없는 현실 속의 현장은 늘 설계와 다르며, 그로 인한 시간과 자재의 로스는 피할 수 없다. 그러나 아래와 같이 가장시운전 작업이 가능하다. 현 시점까지의 시운전 방식과 이후의 시운전 방식은 180도로 달라질 것이다.
시뮬레이션을 활용한 문제해결
현장에서의 시운전은 언제나 장비 업체와 최종 사용자 모두에게 큰 부담으로 다가온다. 아무리 완벽하게 짜인 프로그램이라도 여러개의 제어기가 연동되는 과정에서 예기치 못했던 통신문제가 발생 할 수도 있고, 액추에이터 혹은 로봇의 시운전 중 기구가 파손되거나 작업자 안전이 위협될 수도 있다. 간혹 이미 설치가 된 시점에서 예상치 못했던 작업 흐름의 변경 또한 발생할 수 있다.
이러한 문제들은 결국 언제나 비용의 손실로 이어지게 되고, 시운전 인원의 투입 기간이 늘어날수록 장비 메이커에게는 인건비와 기회비용의 손실로 이어지게 될 것이다. 또한 사용자에게는 양산이 늦어지면 늦어질수록 생산 손실이 될 수도 있을 것이다. 따라서 시운전 시간을 줄이는 방법에 대해서는 현재까지 여러가지 방식이 시도돼 왔다.그 중 대표적인 방법으로 시뮬레이션을 들 수 있으며, 컴퓨터 기반의 설계 방식과 가상 플랜트를 결합해 만들어지는 여러 시뮬레이션 소프트웨어들은 현재까지 자동화 영역뿐만 아니라 우주항공, 군사 등의 분야에 이미 큰 기여를 해왔다.
정해진 시나리오를 따른 생산의 시뮬레이션 혹은 그 과정에서의 문제점 예측을 기구적 충돌 손상이나 안전 문제를 회피하면서도 가상의 공간에서 검증하고, 그 결과를 기초 삼아 현장에 적용해 시운전 착오를 최소화 해왔다. 설비 설치 혹은 생산 요소를 최적화 하는 동시에 인간공학을 도입해 작업자가 최소한의 피로도를 느끼며 작업 할 수 있도록 해 생산성을 높이는 등 지금까지도 많은 일을 해 온 것이 시뮬레이션 기능이다.
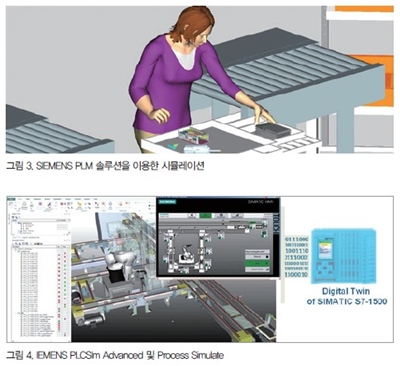
생산라인 전체의 시뮬레이션
기존의 분리 방식의 시뮬레이션과 달리 최근의 PLCSimAdvanced 솔루션은, 센서, 로봇, 드라이브 등에 대해 거의 모든 제약 없이 시뮬레이션 기능을 제공하고, 하나의 시뮬레이션에서 수십개의 PLC와 PLC간 네트워크 연결을 모두 시운전 가능하도록 발전을 이뤘다.
이 두가지의 장점은 사실 간단해 보이지만, 대단히 큰 의미를 갖는다. 기존의 PLC 시뮬레이션 툴들의 경우 거의 대부분이 PLC의 접점 내지는 변수 단위에서의 검증에 초점을 맞추고 있다. 새로운 방식은 시뮬레이션 소프트웨어와 가상 PLC의 완전한 통합을 통해 장비 전체 내지는 생산라인 전체의 시뮬레이션에 중점을 두기 시작한 것이다.
단순하게 로직에 문제가 있는지 없는지 혹은 가상으로 설정한 좌표에 로봇 등의 액추에이터가 문제없이 정해진 시간 이내에 도달하는지 수치로 검증하던 수준을 넘어, 생산 라인을 구성하는 PLC들 간의 통신과 그 데이터의 검증이 가능해졌다. 또한, 액추에이터 및 로봇 등 기구의 간섭을 사전에 배제할 수 있는 검증, 작업 속도와 컨베이어의 구성 방식에 따라 작업자의 특정 신체 부위에 가해지는 피로도를 가상현실에서 하드웨어 없이도 순수하게 소프트웨어를 통해 시뮬레이션하고 검증할 수 있다.
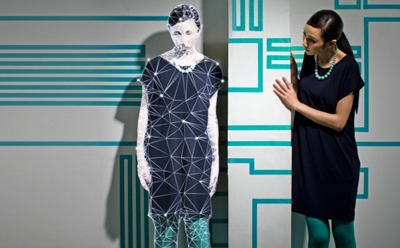
통합을 통한 실시간 시운전
현재까지도 플랜트와 장비의 시뮬레이션 기술은 전반적인 엔지니어링 및 자동화의 역사에서 큰 일꾼 역할을 해 왔다. 이제는 도면 영역을 넘어 자동화 기기들을 거의 제약 없이 시뮬레이션하고, 그 결과를 기구 및 프로그램 요소에 반영하는 위치까지 발전해 왔다.
단수의 PLC 로직의 검증과 기구 내지는 프로세스의 검증을 따로 거치는 과정을 떠나 이제는 프로세스 및 장비의 시뮬레이션과 해당하는 프로그램을 복수개의 PLC 시뮬레이션과 통합해 다양한 조건 하에서 실시간 레벨로 시운전하고, 최소화 된 손실 하에서 가상 시운전 하는 콘셉트는 이미 우리 앞에 있으며, 향후 자동화 기술 요소의 한 축을 이루게 될 것이다.
FA저널 SMART FACTORY 이 건 오 기자 (fa@infothe.com)
<저작권자 : FA저널 SMART FACTORY (http://www.fajournal.com) 무단전재-재배포금지>
저작권자 © 인더스트리뉴스 무단전재 및 재배포 금지