[인더스트리뉴스 최종윤 기자] 복합 구성품 교정 기술에 있어서 누구도 스트레인 게이지 기반 정밀 트랜스듀서 및 측정 장비, 정밀 전자 부품, 힘 및 토크 교정 서비스의 선도 공급업체 중 하나인 GTM의 계측 전문가들에게 필적할 수 없다. 2005년 당시 이미 GTM은 세계 최초의 DIN EN ISO/IEC 17025 인증 복합 구성품 측정 기술 연구소를 보유하고 있었다.
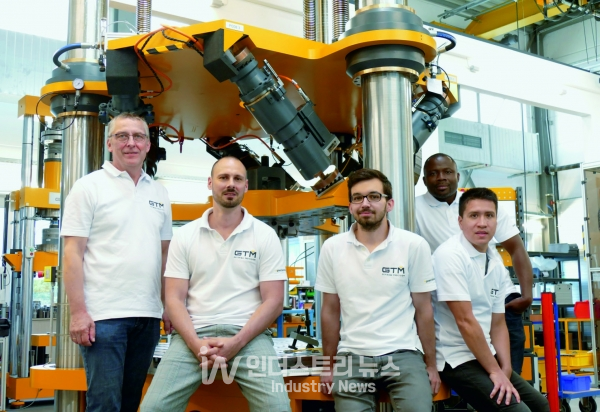
그후 Frankfurt 근처의 Bickenbach에 기반을 둔 GTM은 힘 및 토크 트랜스듀서 뿐만 아니라 복합 구성품 트랜스듀서에 대한 교정 서비스까지 제공해 왔다. 힘의 크기는 개별 구성품에 대해 매우 정밀하게 결정되는 반면에, 포스 어플리케이션 포인트, 힘의 방향 및 레버 암과 같은 기타 변수는 최대한 정밀하게 추산될 뿐이다. 이러한 측정들은 단축 측정 장비에서 이루어진다.
GTM의 관리 이사 겸 기술 이사인 Daniel Schwind는 포스 벡터를 온전히 측정하는 것이 또 다른 방안이라고 얘기하면서 계측학에서 많이 논의되는 두 번째 접근 방식을 언급했다. 이 방식의 이점은 측정 설정이 측정 불확실성의 유일한 원천이라는 점이다. GTM은 완전한 벡터 측정 기술이 장기적으로 PTB(Physikalisch-Technische Bundesanstalt)와 같은 정부 기관에서 그리고 산업 표준으로 정립될 것으로 확신하고 있다.
결과적으로 2005년부터 운영돼 온 수동 복합 구성품 참조 표준 측정 장비와 더불어 새로운 완전 자동 시스템에 대한 투자 결정은 GTM 입장에서 개발과 관련된 논리적인 조치였다.
GTM은 자체 측정 장비로 계측학적으로 어려운 분야로 기술적 경로를 단축했다. 이는 모든 기존 복합 구성품 교정 방법이 해결 가능한 측정 불확실성이든 교정 작업이 요구되는 것이든 어느 정도 취약점을 가지고 있기 때문이다.
Daniel Schwind 이사는 “GTM이 구현한 것과 같이 복합 구성품 참조 표준 측정 장비는 미개척 분야였다”고 설명했다. 따라서 일부 분야에서는 기본적인 연구가 필요했다. 이 비교 측정 및 검증 작업은 측정 장비의 개발 이전에 혹은 어떤 경우에는 개발과 병행해 수행됐다. 교정 연구소 Torsten Hahn 부소장은 “인증 동안 절차 및 우리 측정 장비의 추적성에 대해 평가자와 심의를 거쳤으며 이는 매우 유익한 토론이었다”고 전했다. 측정 장비에 대한 심의는 2016년 중반에 시작됐는데, 당시 복합 구성품 교정에 대한 견적 요청이 기존 교정 절차로는 기존 측정 장비에 대한 모든 주문을 더 이상 충족할 수 없는 수준까지 증가했다. 현재까지 사용되는 수동 교정 프로세스가 시간을 많이 소요해서 교정 대상을 측정 장비에 정밀하게 설치해야 하며 측정 시에 수차례에 걸쳐 위치를 재조정해야 하기 때문이다.
때문에 전체 교정 프로세스는 설치시간이 상당히 오래 걸린다. Marcel Richter 제품 관리 및 마케팅 담당 이사는 “그와 같은 교정 작업에 약 이틀이 소요됐었다”고 밝혔다. 새로운 측정 장비에서는 요구되는 시간이 대폭 줄어든다. 시편을 고정하고, 측정 장비를 교정 대상에 맞게 구성하고, 운영 소프트웨어에서 자동 교정 프로세스를 구성하는 것만 하면 필요한 조치가 모두 완료된다. 제반 구성품의 통합 덕분에 교정 작업은 하룻밤만에 완전히 자동으로 수행할 수 있게 됐다. 이전 프로세스와 비교할 수 없는 큰 이점이다.
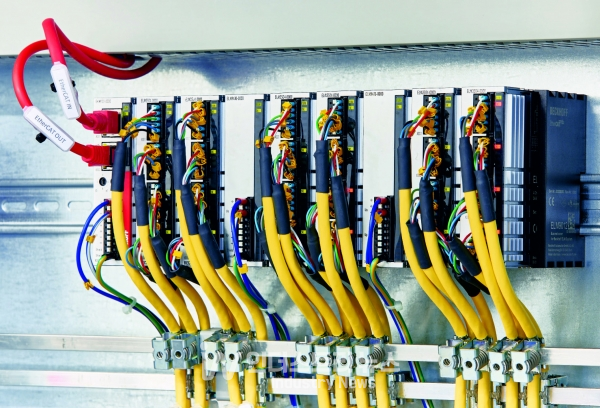
0.5%에서 0.1%로 정확도 개선
완전히 자체적으로 개발된 측정 장비는 교정 작업의 측정 불확실성을 이전 인증 시에 비해 다섯 배나 완화해 준다. 이 덕분에 GTM은 복합 구성품 측정 기술 및 교정 분야의 선도 기업으로 입지를 확고히 구축할 수 있게 됐다. 동시에, 교정 대상에 적합한 현실적이고 어플리케이션 지향적인 설치 조건을 통해 교정 범위 또한 대폭 확대해 왔다. 측정 시스템 팀장이자 책임 설계 엔지니어인 Martin Eller 측정 시스템 팀장은 “필요한 유연성을 확보하기 위해 고객의 설치 현장을 모방한 4.5m3크기의 초대규모 테스트 챔버를 설계했다”고 말했다.
GTM은 측정 불확실성 측면에서도 신기원을 이룩하고 있다. Daniel Schwind 이사는 “GTM은 0.1%의 입증된 낮은 측정 불확실성과 4~500kN(축 방향) 및 2~200kN(횡 방향)의 폭넓은 측정 범위로 교정 분야에서 최고의 기업으로 인정받고 있다”면서, “측정 장비는 2~5 kNm의 토크를 가하고 정밀하게 측정할 수 있다”고 밝혔다. 덧붙여 Martin Eller 팀장은 “그와 같은 낮은 측정 불확실성으로 폭넓은 측정 범위를 구현할 수 있는 또 다른 방법은 단축 측정 장비를 사용하는 것이 유일하다”고 전했다.
이러한 핵심 데이터를 얻기 위해 처음 설치 단계부터 막대한 양의 작업이 투입됐다. 핵심 요소는 교정 대상의 크기와 관련해 유연성을 최대로 보장하는 세 가지 기본적인 측정 플랫폼으로 구성돼 있으며, 새 측정 장비에는 특별히 맞춤 설계된 고정밀 K 시리즈 포스 트랜듀서가 장착돼 있다. 또한 설계 및 제작 단계에서 시중에서는 제어 시스템을 포함한 헥사포드와 같은 적절한 기계 구성품을 찾을 수 없다는 사실을 알게 됐다.
Martin Urbanski 측정 장비의 소프트웨어 개발을 담당은 “이 장치는 당초 구매하기로 계획했었으나 결국 자체적으로 개발해야 했다”면서, “Beckhoff의 PC 기반 제어 및 드라이브 기술을 바탕으로 정밀 측정 전자 부품을 포함해 제반 구성품을 원활하게 통합하는 적절한 고성능 플랫폼을 발견할 수 있었다”고 밝혔다.
측정 장비는 서보 모터와 3개의 스핀들을 통해 교정 대상에 맞게 조정된다. 교정 프로세스 동안 AX8000 다축 서보 시스템 및 AM8042 서보 모터에 의해 구동되는 6개의 나사형 드라이브가 최대 정밀도로 필요한 힘과 토크를 생성한다. Marcel Richter 이사는 “0.1%의 낮은 측정 불확실성 덕분에 차별화를 기하고 사용자들이 자신의 적용 분야를 개선하기 위해 새로운 접근 방식을 취하도록 할 수 있다”면서, “훨씬 더 정밀해진 교정으로 추측이 보다 정확한 측정과 보다 신뢰성 있는 지식으로 바뀌었으며, 이를 통해 GTM 고객들은 공정 및 제조 공차를 더욱 최적화할 수 있게 됐다”고 말했다.
Beckhoff의 Christian Lindemann 정밀 측정 기술 제품 관리자는 “보다 정밀한 복합 구성품 트랜스듀서는 항공업체가 풍동에서 이루어지는 공기 역학 테스트에서 더욱 세부적인 사항을 측정하고 항공기에 대한 수정의 효과를 평가할 수 있게 해준다”고 설명했다. 모델을 조금만 개선해도 항공기 운영 효율을 크게 향상시킬 수 있다. 풍력 터빈의 로터 블레이드, 선박 추진 시스템 또는 자동차 타이어 회전 저항 측정도 마찬가지다.
또 다른 설계상 이점은 GTM이 헥사포드의 6개 축을 통해 임의의 방향에서 중력을 매우 정밀하게 재현하고 사실상 실제 설치 조건에서 고객별 어플리케이션을 교정할 수 있다는 것이다. Daniel Schwind 이사는 “이 솔루션은 다른 곳에서는 사용할 수 없는 고객별 복합 구성품 측정 기술의 트렌드를 완전히 바꾸고 있는 혁신적인 솔루션”이라고 강조했다.
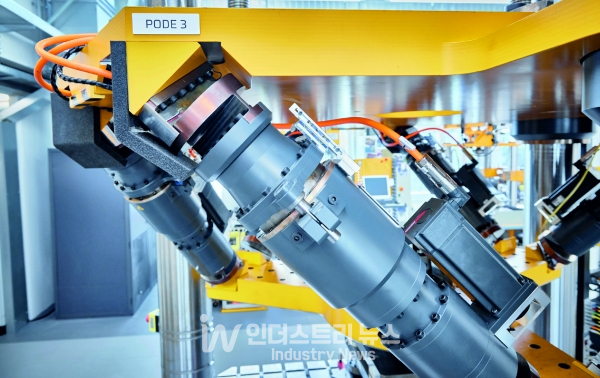
전체 측정 체인에 좌우되는 교정
교정 시퀀스(부하 적용, 부하 해제, 부하 변경, 측정 범위, 반복)는 GTM의 전용 WebForceManager 운영 소프트웨어를 통해 측정 기술자들에 의해 구성된다. 순차적 명령으로 구성된 소프트웨어는 사용되는 교정 시퀀스를 바탕으로 측정 장비를 완전히 자동으로 제어한다. 이러한 명령은 TwinCAT으로 전송돼 추가로 처리된다. 뿐만 아니라, 헥사포드 키네마틱스의 실현 및 모든 측정 신호의 동시 획득과 같은 실시간 요건을 충족해야 하는 프로그램 섹션도 TwinCAT에서 구현된다.
제어 하드웨어의 경우 GTM은 임베디드 PC와 첨단 ELM3504 측정 터미널을 사용한다. 모든 측정 터미널은 6 와이어 기술로 설계된다. 측정 기술은 EKM1101 EtherCAT 커플러 및 ELM9410 전력 공급 터미널에 의해 보완되는데, 둘다 측정 터미널에 대한 양질의 전력 공급을 보장하는 인프라 구성요소다.
Beckhoff의 Christian Lindemann 정밀 측정 기술 제품 관리자는 “GTM이 우리의 산업용 측정 터미널을 매우 면밀히 검토하고 이와 같이 까다로운 교정 시스템에 Beckhoff의 터미널을 선택한 것에 대해 정말 기쁘게 생각한다”면서, “ELM3504 고급 측정 터미널은 기존의 측정 기술 공급자 및 GTM의 자체 측정 전자 장치와의 치열한 경쟁에 직면해 해당 작업에 대한 적합성을 입증해야 했다”고 말했다. Daniel Schwind 이사는 “Beckhoff 터미널을 GTM의 고정밀 포스 센서와 조합했는데, 데이터시트에 명시된 것보다 교정 연구소의 주변 조건에서 훨씬 더 정밀하게 작동한다는 사실을 알게 됐다”고 전했다.
GTM은 당초 EtherCAT이 가능한 자체적인 측정 전자 장치의 개발을 고려했다. 하지만 Daniel Schwind는 ELM 측정 터미널을 직접 사용해 보고 노력을 절감할 수 있었다고 말했다. Christian Lindemann 관리자는 “Beckhoff는 사양에 대해 항상 보수적인 관점을 견지하며 Beckhoff의 구성품이 더 어려운 실제 조건 하에서도 여전히 구현할 수 있을 경우에만 기술 실현을 고객에게 약속한다”고 부연했다.
헥사포드를 통해 힘 및 토크 투입량을 기록하고 교정 대상을 측정하는 데 총 6개의 4채널 ELM 고급 측정 터미널이 측정 장비에 사용된다. EL 시리즈의 EtherCAT 터미널도 추가로 사용된다. 측정 장비에 사용되는 전자 구성품 담당자인 Holger Schneider는 Beckhoff 터미널의 표준 해상도가 이에 완벽하게 호환된다고 강조한다.
이들은 특히 스트레인 게이지를 통해 액추에이터가 최대 힘에 적합한지 모니터링하는 데 사용된다. 6개의 헥사포드 실린더는 서보 드라이브 및 AX8000 다축 서보 시스템에 의해 구동된다. 마찬가지로 GTM이 자체 개발한 동력 전달 시스템에는 기어박스와 스크류 드라이브가 포함된다.
그 결과 상대적으로 작은 서보 모터가 최고 수준의 정밀도로 높은 힘과 토크를 생성했다. Martin Eller 팀장은 “Beckhoff의 소형 다축 시스템과 PC 기반 제어 및 EtherCAT을 통한 측정값 데이터의 실시간 동시 전송의 조합이 여기에서 도움이 된다”면서, “덕분에 측정값을 바탕으로 모든 드라이브 제어 작업을 간소화할 수 있게 됐다”고 설명했다.
선택된 제어 아키텍처는 컨트롤 캐비닛 등 다른 시스템에도 긍정적인 효과를 보여주고 있다. GTM이 측정 증폭기 및 기타 I/O 구성품에서 산업용 PC 및 드라이브 기술 제품까지 거의 모든 구성품을 Beckhoff로부터 조달하고 있기 때문에, 전자 장치/부품을 전반적으로 훨씬 더 간소화할 수 있었다.
Holger Schneider 담당자는 “개별 서보 및 측정 기술 제품을 여러 공급업체로부터 조달한다는 당초 계획을 고수했다면 3대의 컨트롤 캐비닛이 필요했을 것”이라고 밝혔다. 각기 다른 시스템에 요구되는 통합 및 엔지니어링 작업은 두말할 필요도 없다.